01
Sep
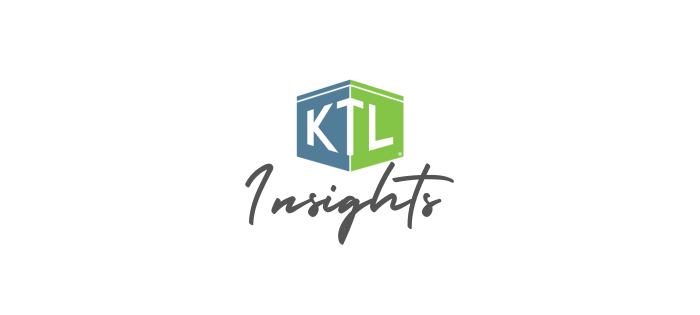
Environment / Safety
Comments: No Comments
The discipline required to design and implement a compliant environmental, health & safety (EHS) management system can help organizations improve in many areas over and above the tasks, as defined.
- Identify and categorize the organization’s EHS risks. Once this information is known, management will be able to prioritize and then pick and choose how to reduce risks and liabilities to acceptable levels. These risks will be better controlled through strict management accounting. Employees will become more attuned to thinking outside the box to help management improve the overall operation.
- Develop work instructions and/or procedure to guide an employee’s actions and ensure that each EHS task is completed in a disciplined manner approved by management. This will reduce the risk to an organization of an employee accidentally making an environmental, health and/or safety mistake that causes the employee or others to be injured or worse; creates public awareness of the problem; or causes governmental inspections, fines, and loss of business.
- Provide management assurance that the company does, in fact, know and understand the legal and EHS requirements that the business must meet on a daily basis. These legal requirements will drive improvement in having up-to-date procedures and work instructions for employees to follow every day.
- Develop meaningful EHS goals and objectives. These objectives drive improvement in environmental and personal health & safety performance. They may also reduce internal costs by reducing trips to the hospital, payments for workers compensation, and employees on disability. Each business will have different goals that should change each year to ensure continuous improvement over time.
- Develop a strong training program. Well-written procedures and work instructions help define the actions required of employees to meet EPA and OSHA requirements and company directives. A well-trained workforce is a motivated and happy work force. Turnover is reduced, accidents and incidents are reduced, and production efficiencies increase. Employees are very aware when an organization takes time to assure each job requested is completed in the safest and most environmentally sound manner possible.
- Develop appropriate monitoring and measurement of key characteristics and requirements. These key performance indicators are based on regulations and laws intended to guide the organization’s actions in a direction of continuous improvement and compliance.
- Allow employees to audit and verify that the EHS management systems are functioning as designed and implemented. By continuously auditing each OSHA program and environmental function, the organization will discover issues of concern and non-conformances prior to an employee being injured or worse, having an environmental spill or incident, or incurring a governmental agency finding. This allows the company to choose a timeframe that will best help improve the situation without undue influence by outsiders.
- Design a fully functioning corrective/preventive action program to monitor issues of concern and/or non-conformance and the actions used to rectify each situation identified. As employees watch management fix problems, they will learn that management is concerned about continuous improvement and the employees will go back to making improvement suggestions. These suggestions will further drive improvement in areas outside the original EHS management systems.
- Look at the business model and the EHS management systems in a holistic fashion. By using this self-reflection and identifying improvement opportunities, management can direct responsibilities for improvement actions across many departments within the company. Each of these improvement opportunities will again help the bottom line and reduce the possibility of an EHS liability now or in the future.
- Know that you have done everything possible to maintain the business in a manner to meet all OSHA and EPA rules and regulations, as well as association requirements. The organization will have done everything possible to assure that the environment and the health & safety of employees are protected every day the doors are open for business. To a business owner, that knowledge is priceless.