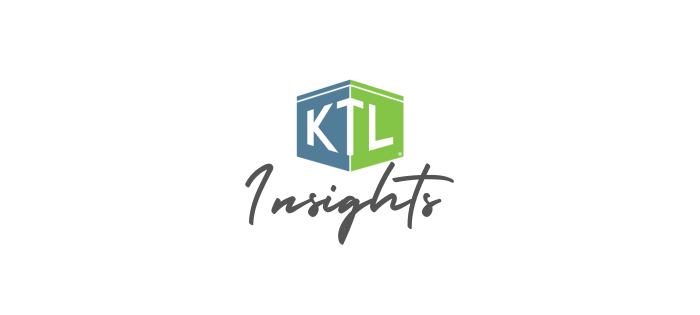
Kestrel Tellevate News
Comments: No Comments
On August 6, 2012, a release of flammable vapor led to a fire at the Chevron Refinery in Richmond, California. That event generated significant public concern about refinery safety and emergency response in California. It also prompted the California Governor’s report, “Improving Public and Worker Safety at Oil Refineries,” the formation of the Interagency Refinery Task Force (IRTF), and, eventually, the proposed regulatory changes to specifically target refinery safety.
Proposed Cal/OSHA Process Safety Management (PSM) Standard Changes
As most California refineries are aware, California’s Department of Industrial Relations (DIR) developed a draft regulatory proposal for a new Cal/OSHA Process Safety Management (PSM) standard to strengthen regulatory oversight, policy, and enforcement. The PSM for petroleum refineries notice hit the California Register on Friday, July 15, 2016—and Federal changes are on the way, as well, as OSHA considers revisions to its PSM standard.
As a recap, the proposed Cal/OSHA PSM changes modify existing PSM language and introduce a number of new management system elements and other requirements. These amendments require California refineries to commit to the following:
- Use the Hierarchy of Hazard Controls to choose safer, more enduring technologies that address safety concerns and help to eliminate or minimize hazards in refinery processes.
- Perform damage mechanism reviews to assess physical degradation, such as corrosion and mechanical wear, and to determine recommended corrective actions.
- Conduct safeguard protection analysis to ensure that safeguards will help prevent initiating events from turning into major catastrophes.
- Implement corrective actions with clear and enforceable deadlines and consequences for inaction to ensure that safety program improvements are carried out.
- Implement appropriate Management of Change (MOC) activities so safety is factored into changes to operations, maintenance procedures, personnel, etc., all of which can undermine plant safety.
- Perform periodic safety culture assessments to evaluate management’s and employees’ attitudes, perceptions, and values as they pertain to safety.
- Account for human factors (e.g., training and competency levels, fatigue, experience, communication, physical challenges), which can greatly influence accidents and incidents in the workplace.
- Conduct root cause analysis to identify underlying causes of the incident and recommended corrective actions to help prevent recurrence.
- Engage employees at all levels in all elements of the PSM program, including working to prevent accidents and incidents through the means described above.
The Human Element of PSM
Employee and contractor performance is a significant source of risk within any organization. The majority of accidents and other unintended events are—at least in part—the result of human error. It is not surprising that Cal/OSHA’s proposed PSM regulations recognize the importance of the “human element” in a number of the proposed changes—from performing safety culture assessments, to account for human factors, to engaging employees.
Kestrel works with many refining and petrochemical companies that are in the process of establishing and/or improving elements of their PSM programs. Over the years, we have seen many of our clients struggle with the following challenges:
- How do we identify factors contributing to incidents?
- What are appropriate recommendations that will drive improvements?
- How should we include human factors in Process Hazard Analyses (PHAs)?
- How can we improve our safety culture?
Often, these elements are treated independently, but we have found that this overlooks the important relationship between them. For example, any unintended event (e.g., an LOPS, process upset, safety incident) is the result of multiple contributing factors, not a single event. Focusing on these contributing factors enables companies to develop a deeper understanding of why incidents are occurring. Linking contributing factors to specific barriers further allow companies to identify weaknesses in their procedures and processes and to develop appropriate recommendations to drive improvements. Conducting contributing factor analyses also enables the company to identify specific human factors to be used in their PHAs.
Human Performance Reliability (HPR) Approach
Kestrel’s Human Performance Reliability (HPR) approach provides an integrated solution for addressing the new PSM requirements, as outlined above. Unlike a typical root cause analysis, which addresses factors leading to a specific incident, HPR is based on a sophisticated statistical analysis of human factor data obtained from multiple incidents. This allows companies to identify and access broader—and potentially systemic—issues that are affecting the safety performance of the organization.
HPR consists of three elements:
- Incident Investigation and Analysis (IIA) – IIA adopts the framework provided by the Human Factors Analysis and Classification System (HFACS) to classify human error and other contributing factors—but with the additional step of associating the control(s) that failed to prevent the incident from occurring. Statistical analyses help to identify patterns in the data to pinpoint the human errors and controls that are appearing most frequently.
- Procedure Improvements – Although the IIA process will identify where improvements are needed (i.e., which controls are associated with incidents), it will not result in performance improvements—not without completing associated improvement projects. As part of our HPR services, Kestrel works with clients to scope and implement those improvement projects that will lead to improved safety performance.
- Safety Culture Assessment – Learning organizations actively seek the underlying causes of incidents and use data to make performance improvements. These organizations typically have robust systems to ensure that the traits that represent a strong safety culture are in place, mature, and fully integrated into standard practices.
While the individual elements can be very helpful to a company, deploying them in tandem provides the richest and most comprehensive benefit to overall safety performance. That is because the three components are inherently complementary; each improves the effectiveness of the others.
Systemic Improvements
The HPR process provides immediate value when applied to the investigation of an individual event by identifying additional factors that may have been missed following a traditional root cause analysis approach. It is most powerful, however, when data from multiple events are aggregated. The results of multiple investigations yield a pattern of human factor indicators that can be used to uncover system opportunities for PSM and operational enhancements and overall improved reliability.
Experienced Professionals
Kestrel has experienced PSM and HPR professionals on our team, who have successfully developed programs, completed deployments, and conducted training in the refining and petrochemical industries. As California refineries prepare for significant PSM regulatory changes, we would welcome the opportunity to discuss how we can help you manage your PSM requirements and improve your overall safety performance.